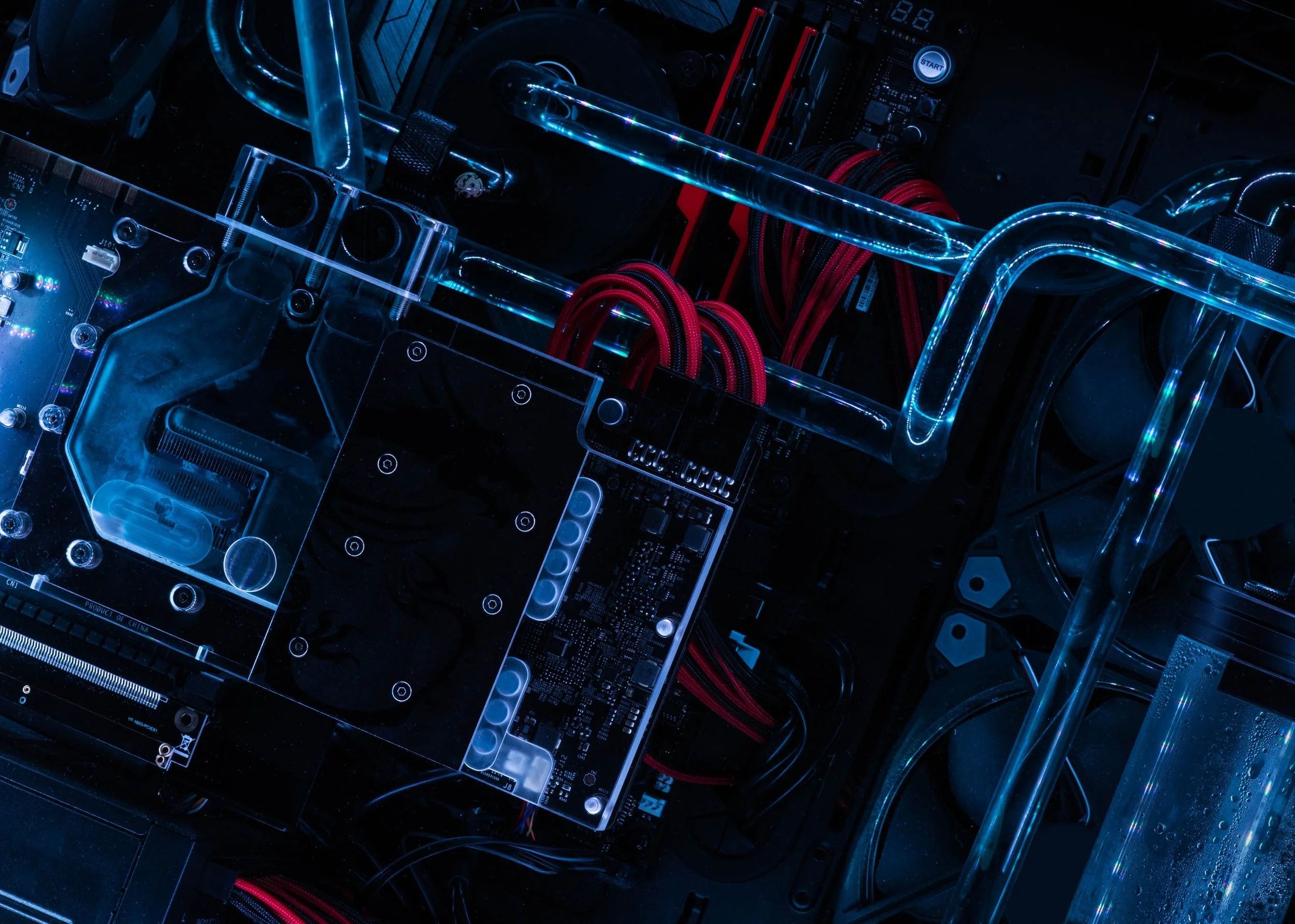
x3 1.2mW water-cooled chiller replacements for a client in London
Working alongside six project partners and nine subcontractors, we successfully replaced three 1.2mW Carrier water-cooled chillers under challenging traversal and spatial conditions.
Our client wanted to replace the site’s chiller plant and associated components as they had come to their end of life.
This consisted of x3 carrier water cooled chillers, x2 primary chilled water belt driven pumps, x2 secondary chilled water belt driven pumps and x2 condenser water belt driven pumps, all located in the basement. Also included was a full refurbishment of the x2 Baltimore cooling towers on the roof of the premises.
Due to the age of the existing system and numerous changes to its design over the years, we completed a full validation of the chilled and condenser water system. We used what was left of the original O&M’s to check the flow rates and system capacity were correct.
Our water treatment partner completed a number of water sample analysis tests of both the chilled and condenser water systems throughout the project.
Flushing of both the chilled and condenser water systems was also undertaken as part of the plant replacement.
Replaced x3 1.2mW water-cooled chillers
First stage of project included dismantle and removal of all obsolete plant waste, which generated 35 tonnes of waste metal
We used 10-tonne hydraulic jacks and beams to lift the chillers
Chillers were manually rolled from the plant room to a larger site
All components has to be brought up/down ramps using winches
All components removed were fully recycled
X6 new inverter drive pumps were installed
We employed a specialist consultant to cross check our validation results. They then completed a detailed design of new system to include the new chillers and new pumps.
The consultant also provided drawings and a full specification that was submitted to the customers surveyors and consultants.
The three new carrier chillers were stripped down away from site by the manufacturer. All three were delivered individually on Hiab’s and unloaded at the top of the ramp to the basement. We subcontracted a specialist plant movement company to assist with the lowering of the new chiller into the basement area. We then rebuilt the chillers on behalf of the manufacturer.
After all three chiller were positioned they were rebuilt, pressure leak tested, evacuated to remove moisture and charged with refrigerant. All electrical components were fitted and connected. Both the chilled water and condenser water pipework was installed, pressure tested and insulated. The chillers fitted inside of the plant room perfectly. All were placed on made to measure concrete plinths.
The main constraints with the project was the location of the existing chiller plant room and how to replace the obsolete equipment.
We were able to draw on a large supply chain to support us with solutions for all of the components and materials required to complete the project.